We received an engineering project in the Philippines, where the client requires 100W all-in-one solar street lights with a lamp body weight exceeding 30kg and an installation height of 12 meters.
Taking into account the local climate conditions, degree of seawater corrosion, expected lifespan, and load-bearing requirements, we believe that galvanized aluminum material, with its lightweight, corrosion resistance, and high structural strength, is suitable for this project. We decided to manufacture the light poles with 4mm thick aluminum sheets.
The manufacturing process for aluminum lighting poles is as follows:
1. Prepare the galvanized aluminum sheet of the required thickness in advance, typically ranging from 2 to 4mm thick.
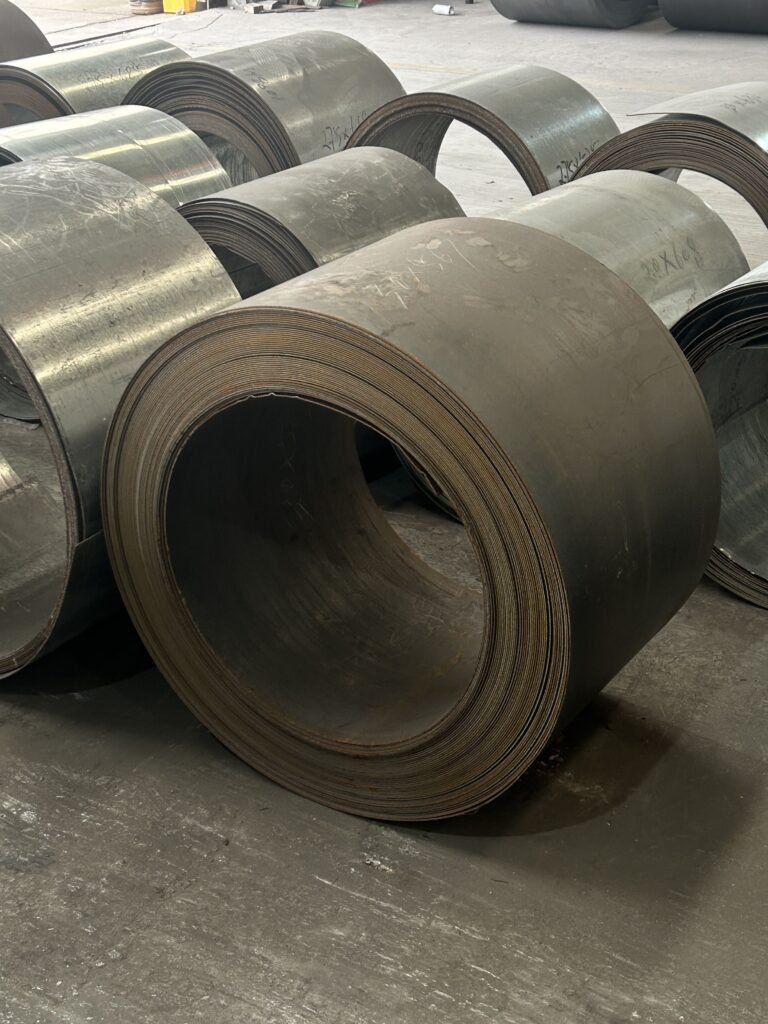
2. Place one side of the aluminum sheet onto the aluminum sheet correcting machine to flatten the originally curled aluminum sheet.
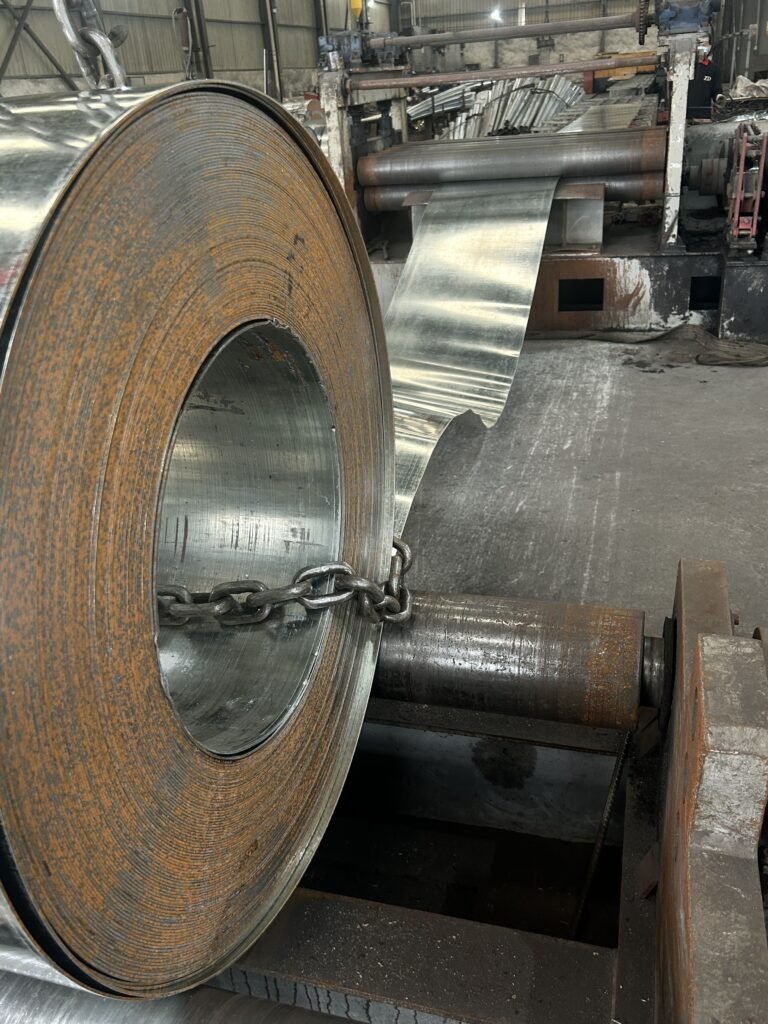
3. Cut the flat aluminum sheet into the required width and length.
4. The cut aluminum sheets are pressed into near-cylindrical shapes by the aluminum plate rolling machine and then welded together using an automatic welding machine to form the lamp post.
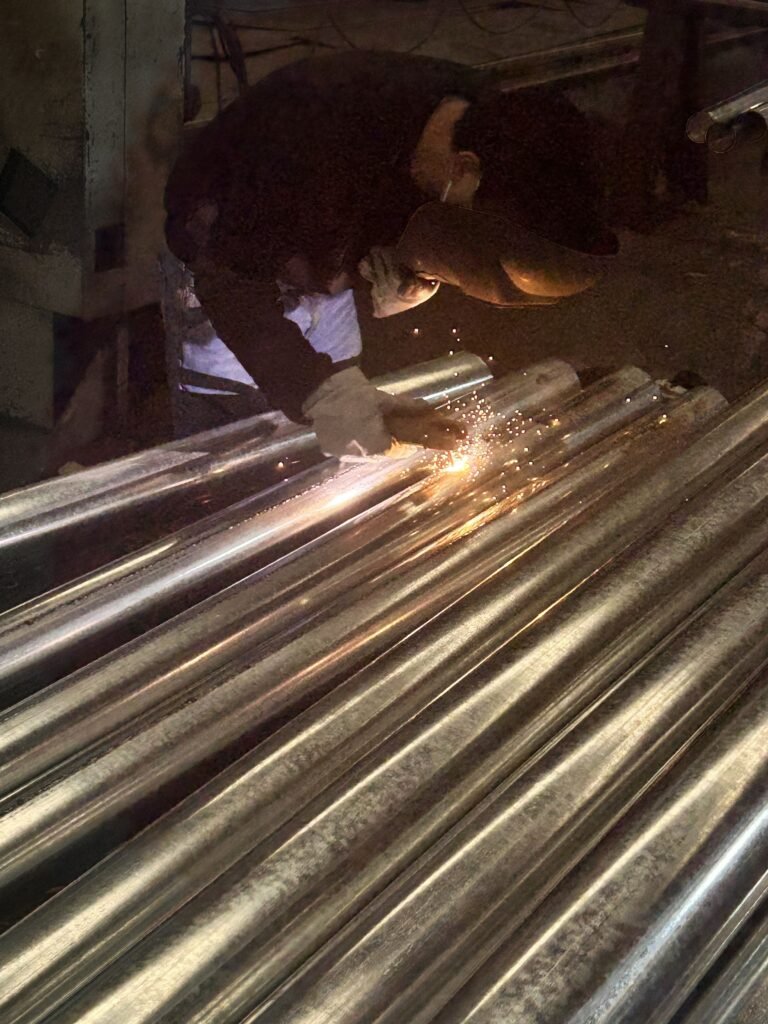
5. For anchor base poles, the base plate is then welded to the pole at the top and the bottom of the plate.
6. Weld the base to the bottom of the pole, and then cut hand holes and mounting holes on the pole.
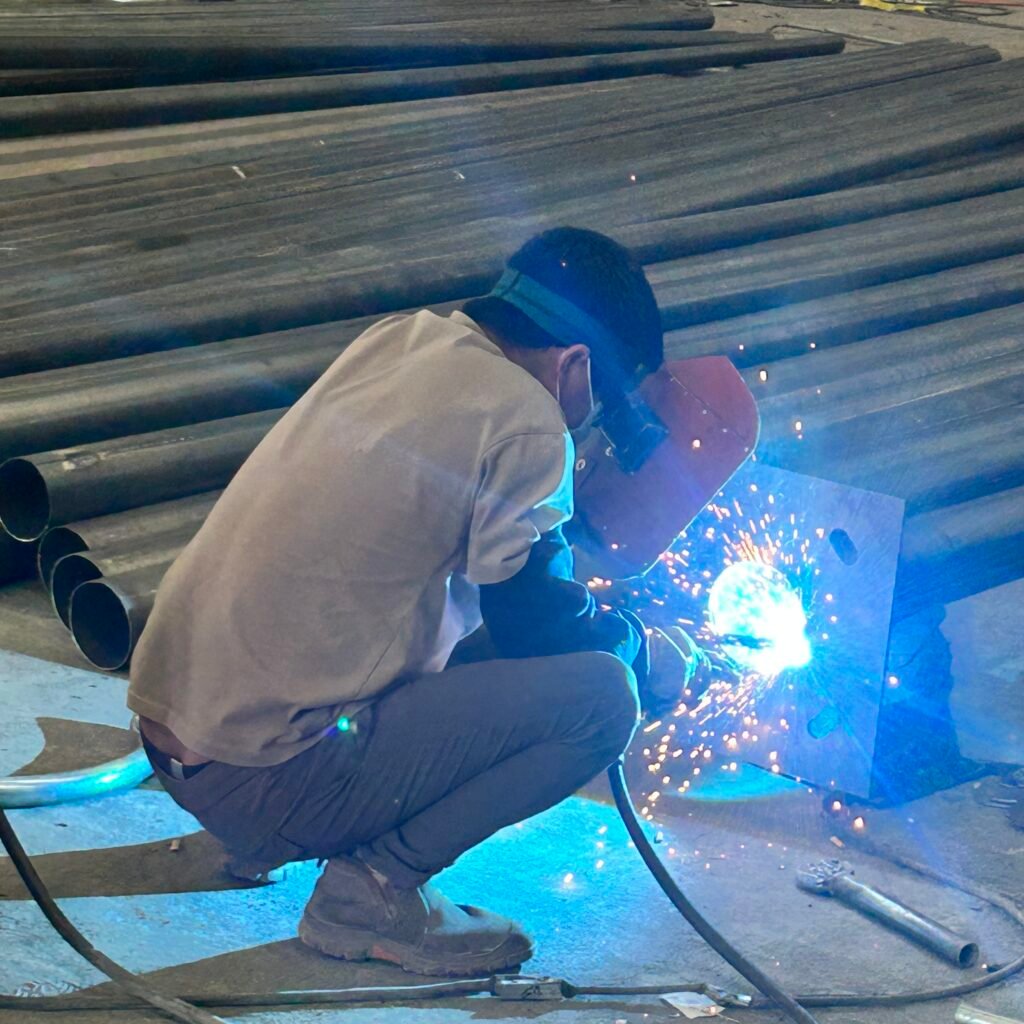
7. Anodize or powder-coating the lamp post to enhance its weather resistance and corrosion resistance.
We have rich experience in project plan design. If you have any project consultation, please feel free to contact us for free solution planning services.