To understand the quality of a solar lamp, we first need to know what parts it is composed of, and what methods and tools are used to understand whether the quality of these parts is good or bad.
Solar lights consist of photovoltaic panels, batteries, LED lamp beads, lenses, controllers, light fixtures and connecting cables.
Introduction of Each Component
SOLAR PANEL
Photovoltaic panels are divided into monocrystalline and polycrystalline photovoltaic panels. Compared with polycrystalline photovoltaic panels, monocrystalline photovoltaic panels are darker in color, have higher power generation efficiency, and are more expensive.

BATTERY
Batteries are usually lithium-iron phosphate batteries, also called LiFePo4. Compared with other battery types (lead-acid batteries, nickel metal hydride batteries, lithium-ion batteries), LiFePo4 batteries have a high energy density, lightweight, good safety, long battery life, low self-discharge rate, and lower merits. It is the best option for outdoor solar lights for the moment.
LED Chips
The mainstream models of LED chips include 2835, 3030, 5050, and 5054. The numbers in the model represent the dimensions of the LED chip, for example: 2835 refers to a square LED package with dimensions of 2.8mm by 3.5mm.

What is the power range of these 4 different LED chips?
Model | Description |
2835 | The power of a single LED chip is usually between 0.2 watt and 1 watt. |
3030 | The power of a single LED chip is usually between 0.2 watt and 2 watt. |
5050 | The power of a single LED chip is usually between 0.5 watt and 1.5 watt. |
5054 | The power of a single LED chip is usually between 0.5 watt and 2 watt. |
P.S.: The larger the chip size, the higher the price. If a single LED chip needs to have a power of 1W, choosing 2835 would be more cost-effective than 3030. However, due to the smaller chip size of 2835, the maximum luminous efficacy can only reach up to 170 lumens per watt, while opting for 3030 LEDs can achieve a maximum of 210 lumens per watt.
Lense
PC material is the best choice for lenses, offering excellent light transmission, high weather resistance, impact resistance, lightweight properties, and high design freedom.
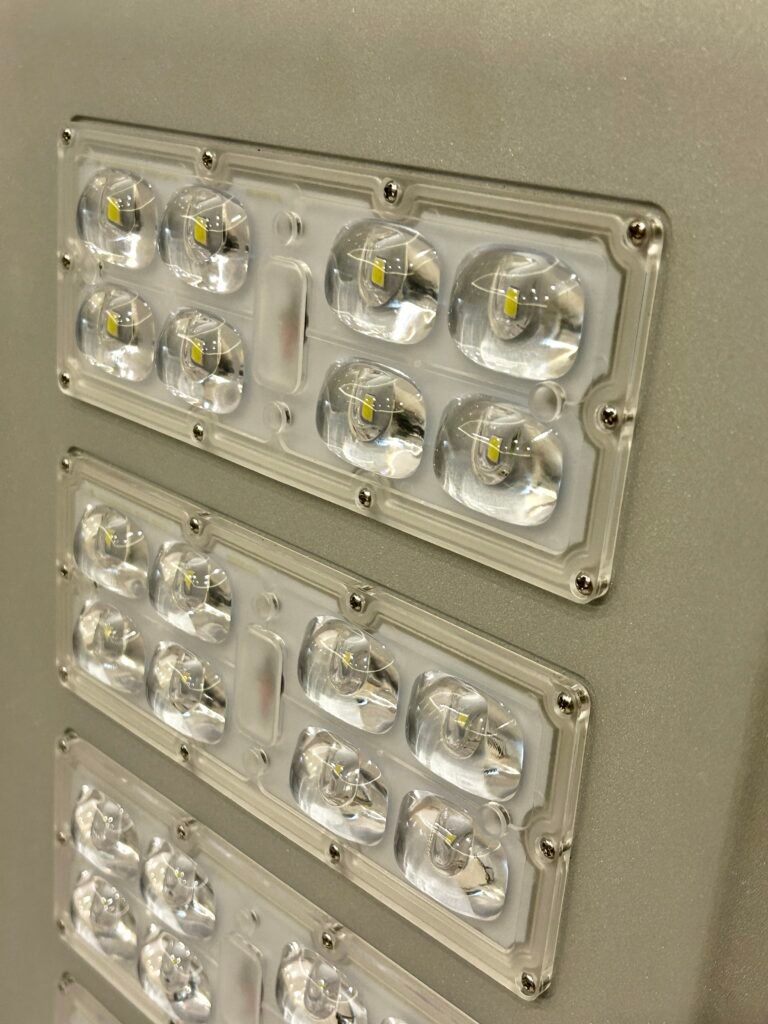
Controller
The most popular types of solar light controllers are PWM (Pulse Width Modulation) and MPPT (Maximum Power Point Tracking).
- PWM controller: A PWM controller regulates the voltage output of a solar panel by rapidly switching the solar array between fully charging the battery and letting the battery sleep, thus maintaining a constant voltage.
- MPPT controller: The MPPT controller maximizes the charging efficiency of solar panels by continuously tracking and adjusting the operating point of the solar array to match the maximum power point (MPP) under varying weather conditions.
Light Fixture
There are 3 main materials for solar lights: PC plastic (Polycarbonate), iron, and aluminum.
Pros & Cons | PC Plastic | Iron | Aluminum |
Pros | Weather resistance Impact resistance Design flexibility Cost-effective | Strength Affordability Rust Resistance (with good coating) | Lightweight Corrosion resistance Aesthetic appeal |
Cons | Scratch prone Heat sensitivity | Heavy weight Susceptibility to rust (without good coating) | High cost Strong heat conductivity |
Exposure to sunlight for extended periods can cause surface aging of PC plastic, resulting in roughness, whitening, or cracking. Its strength may decrease, making it more fragile and susceptible to cracks or damage. So iron and aluminum materials solar lights are more suitable for outdoor use.
The problem is the production cost. The best solution is to balance the quality and the cost of iron solar street lights.
You can check more information via this article: The Superiority of Iron Solar Lights
Connecting Cables
The connecting cable of solar lights typically consists of insulated wires that connect various components of the solar light system, including the solar panel, battery, LED light, and controller.
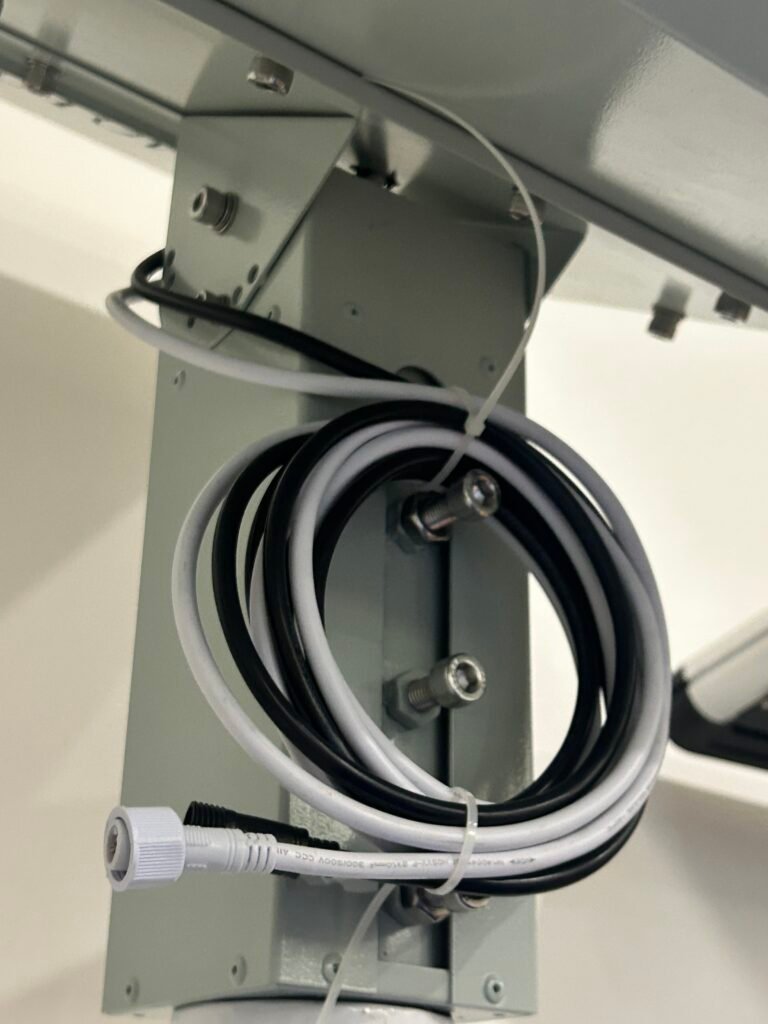
How do I check the quality of solar light components?
In this comprehensive guide, we’ll delve into the essential factors to consider when assessing the quality of solar lights.
1. Charging Capacity of The Solar Panel
The factors that affect the charging efficiency of photovoltaic panels are mainly the area of the photovoltaic panel (number of photovoltaic cells) and the quality of the photovoltaic cells.
Solar Panel Wattage = Area (in square meters) × Solar Irradiance (in watts per square meter) × Efficiency (as a decimal) x Derating Factor (the loss when transforming light energy to electrical energy)
What is solar irradiance?
Solar irradiance is the power received per unit area from the Sun and can vary depending on factors such as location, time of day, and weather conditions. A typical value for solar irradiance under standard conditions is around 1000 watts per square meter (W/㎡).
In the above formula, the area can be calculated by measuring the length and width of the photovoltaic panel, and the efficiency and derating factor are related to the quality of the photovoltaic panel.
How does the area of solar panels affect charging efficiency?

For example, the picture above is Gcots 30W all-in-one solar street light SL-AIO-QTZ30, the length of the solar panel is 1.15 meters and the width is 40.5 centimeters, with an efficiency of 22%, assuming the derating factor is 0.8, you can estimate the wattage as follows:
1.15m*0.405m*1000W/㎡*22%*0.8≈82W
This means that this photovoltaic panel can generate 82 watt hours of electricity per hour under good lighting conditions. And in fact, this panel is 80W.
Therefore, larger solar panels yield higher charging output power.
But please keep in mind that this is just an estimate when you calculate a solar panel’s wattage, and the actual wattage may vary depending on factors such as the specific conditions at the installation site and the quality of the solar panel.
The quality of the solar panel:
In addition to judging the quality of photovoltaic panels with the naked eye, you can also use electroluminescent (“EL” in short) equipment to detect them.
How do you judge the quality with eyes?
Qualified photovoltaic panels should have no cracks, oxidation, bubbles, and other adverse conditions, and no obvious scratches to the naked eye.
However, some photovoltaic panels appear to be intact to the naked eye, but when captured by the camera of the electroluminescent device, it can be seen which cells are no longer working or have low charging efficiency.
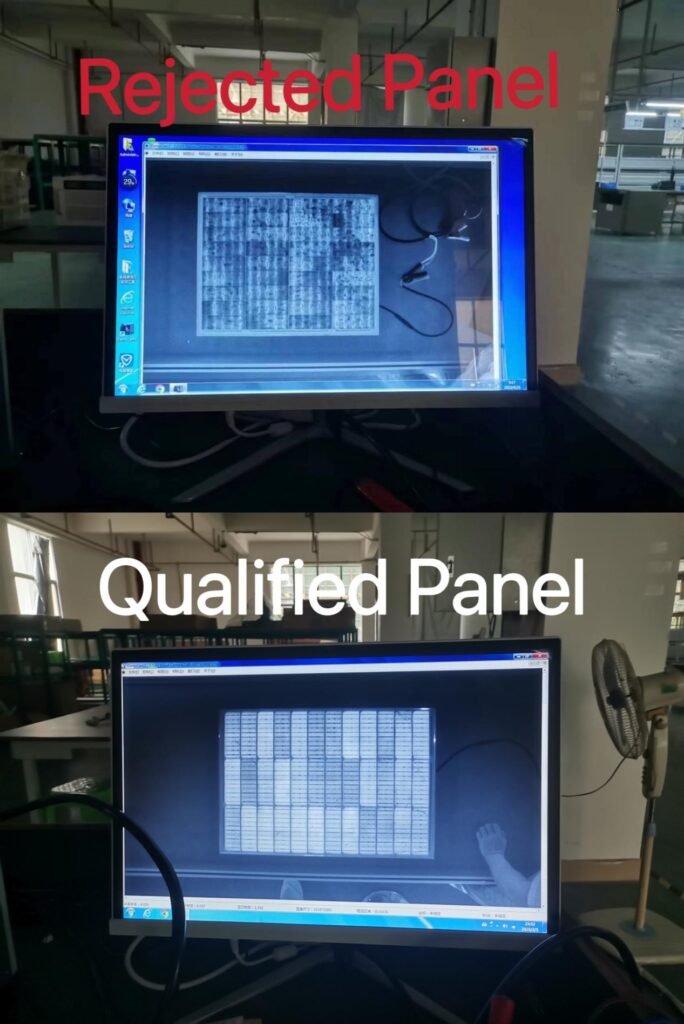
A good solar panel should appear white without noticeable scratches, damage, or cracks. This condition indicates that the surface of the photovoltaic panel should be kept clean, free from significant dirt or damage, and with good reflective performance.
If you are a solar light importer, you must make sure your suppliers have an EL test machine. Without this equipment, they can not inspect the quality from their upstream suppliers. Because they do not produce panels on their own.
Once during the order delivery process, our factory received photovoltaic panels from the supplier that looked flawless to the naked eye, but the actual power tested in the EL equipment was generally 10W lower than what we required.
So if your suppliers do not have an EL test process, all their promises on panels’ quality are bullshit!
2. Battery Capacity, Matching and Protection System
The two main factors that affect the quality of a battery are its actual capacity and whether it has protective measures.
Battery Capacity Test Process
a. Prepare The Battery:
Ensure the battery is fully charged before testing. If the battery is not fully charged, allow it to charge using sunlight or an external power source until it reaches maximum capacity.
b. Set Up The Test Environment:
Establish a controlled testing environment to prevent external factors from affecting accuracy, ensuring consistent conditions such as temperature (25 degrees Celsius), humidity (50-60%), air pressure, light, and electromagnetic interference for reliable results.
c. Connect The Battery Tester:
Connect the positive (+) and negative (-) terminals of the battery to the corresponding terminals on the comprehensive aging tester.
d. Measure Open Circuit Voltage (OCV):
Measure the battery’s open circuit voltage (OCV) using the tester. OCV represents the voltage of the battery when not under load. The voltage of a fully charged battery should be close to its rated voltage.
e. Monitor Voltage Drop:
Monitor the voltage drop across the battery terminals when a load is applied. The voltage should remain relatively stable during discharge, indicating good battery capacity.
f. Record Discharge Characteristics:
Record the battery’s discharge characteristics, including periodic voltage levels and total discharge time. Compare these values with the battery’s specifications to assess its capacity.
g. Calculate Capacity:
Calculate the battery’s capacity based on the recorded discharge data. Capacity is typically measured in ampere-hours (Ah) or watt-hours (Wh), representing the energy the battery can store and provide.
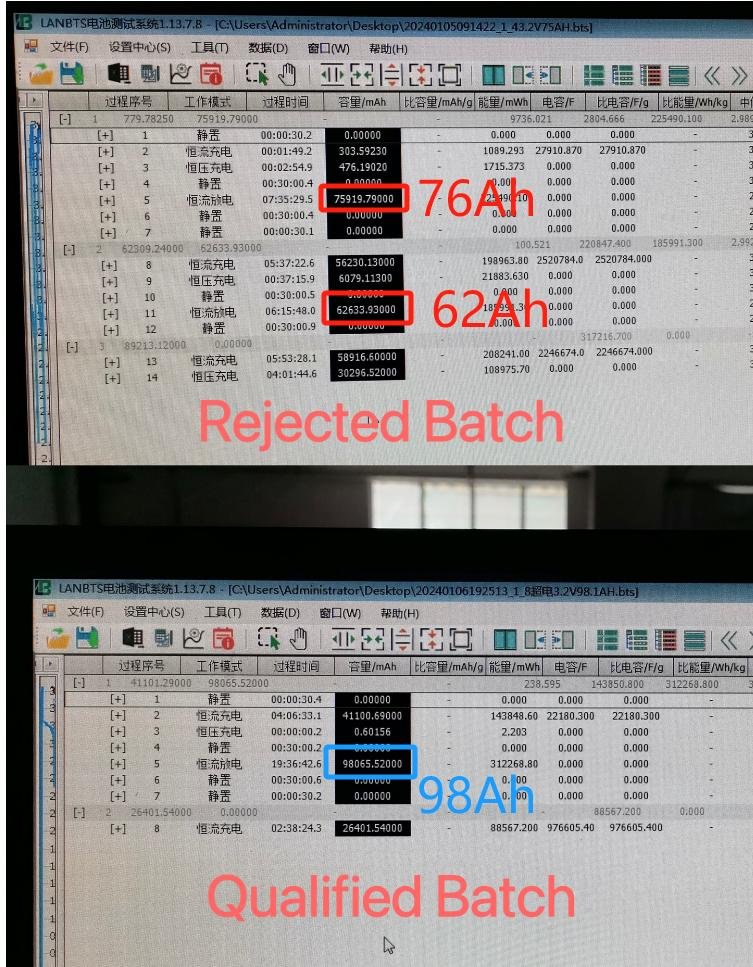
h. Perform Repetitive Testing:
Repeat the testing process multiple times to ensure consistency and reliability of results. This helps identify any changes in battery performance and ensures accurate capacity assessment.
i. Evaluate Results:
Evaluate the test results to determine if the battery meets the expected capacity specifications for the intended application. Compare the measured capacity with the manufacturer’s specified capacity and industry standards to assess quality and performance.
j. Document Findings:
Document the testing procedures, results, and any observations or anomalies encountered during the testing process. This information provides valuable feedback for improving battery quality and manufacturing processes.
A responsible solar energy supplier should strictly implement the above steps.
Battery Matching
Most wholesale solar lights utilize refurbished batteries due to cost constraints, with brand-new batteries reserved for high-end products.
Refurbished batteries undergo capacity matching to ensure uniformity among cells within the pack, promoting balanced performance and extending the overall lifespan.
Variations in battery capacity due to manufacturing processes and environmental factors necessitate capacity assessment and comparison, aiming to minimize discrepancies for optimal pack performance and stability.
This is typically achieved through matching batteries with similar capacities or employing balanced charging methods.
For more information, you can refer to this article: “Cell Matching and Balancing”
Battery Protection
A qualified solar light battery should be equipped with a Battery Management System (BMS) to provide overcharge, over-discharge, over-current, reverse current, over-temperature, and short-circuit protection. This ensures that the battery remains undamaged during long-term use.
3. Optical Parameters of LED Chips
The main optical characteristic parameters of LED chips include color temperature, color rendering index (CRI or RA), color deviation, luminous efficiency, luminous flux, and power. What do they each mean?
- Color Temperature (CCT): Measures the relative warmth or coolness of light emitted by a light source, typically measured in Kelvin (K). Higher color temperatures tend to appear bluer, while lower color temperatures tend to appear redder.
- Color Rendering Index (CRI or RA): The degree of color reproduction in an object illuminated by a light source. CRI values range from 0 to 100, with higher values indicating better color rendering. For road lighting, excessively high CRI is not advisable as it lowers light efficiency, impacting brightness. CRI over 70 can meet the needs of road lighting.
- Color Deviation: Measures the degree of difference between the color emitted by a light source and that of a standard light source. A lower color deviation indicates less difference between the emitted color and the standard color.
- Luminous Efficacy: Measuring the efficiency of a light source in converting electrical power into visible light, typically expressed in lumens per watt (lm/W). Higher luminous efficacy values indicate that LED chips of the same power output produce higher brightness and can be more energy-efficient. This can also lead to cost savings when designing battery capacity.
- Luminous Flux: Measures the total amount of light emitted by a light source, typically expressed in lumens (lm). Higher luminous flux values indicate a brighter light output.
- Power: The electrical power consumed by a light source, typically measured in watts (W). Higher power values indicate greater electrical energy consumption by the light source.
The parameters mentioned can be evaluated for quality compliance by integrating sphere testing of LED chips.

For your reference, we, Gcots will do 2 times of integrated sphere testing. The first time is for the LED chips, the second time is for the whole solar lights.
4. The Quality of A Solar Lamp Lens
To determine whether a lens meets the requirements, we mainly observe whether its beam angle meets the specifications. If the angle is too narrow, it may not meet the requirements. Therefore, we typically use a spectroradiometer to test the entire lamp for spectral distribution.
Then, we can obtain a luminous Intensity Distribution Curve based on the data to determine if a lens replacement is necessary.
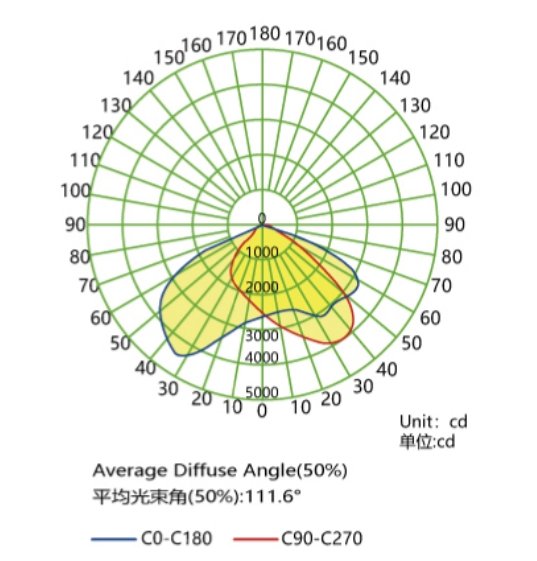
5. How to Check The Working Mode of The Controller?
Different solar light manufacturers have the capability to customize the operating modes of their produced fixtures.
However, this customization requires that the controller is independently designed and developed. If a manufacturer utilizes controllers provided by suppliers, customization and modifications may not be feasible.
Taking our GCOTS as an example with our self-developed MPPT controller, we would implement the following settings: if the illuminance is ≤5 lux and lasts for more than 10 seconds, the solar light will automatically turn on, then operate according to the dimming mode set for each product for 12 hours.
Taking the working mode of one of our solar street lights as an example, its dimming mode is as follows:
Working Time | Maximum Brightness Percentage |
0-20 minutes | 100% |
20-120 minutes | 80% |
2-3 hours | 70% |
3-4 hours | 60% |
4-5 hours | 50% |
5-6 hours | 30% |
7-12 hours | 20% |
We will place the solar lights in an area where direct sunlight is not available to simulate rainy day conditions, requiring the lights to operate continuously for 3 days, which is 36 hours in total.
This is our GCOTS standard for testing the controllers’ performance. However, specific requirements may vary, and it’s essential to communicate these requirements with your supplier.
6. What Is A Good Light Fixture?
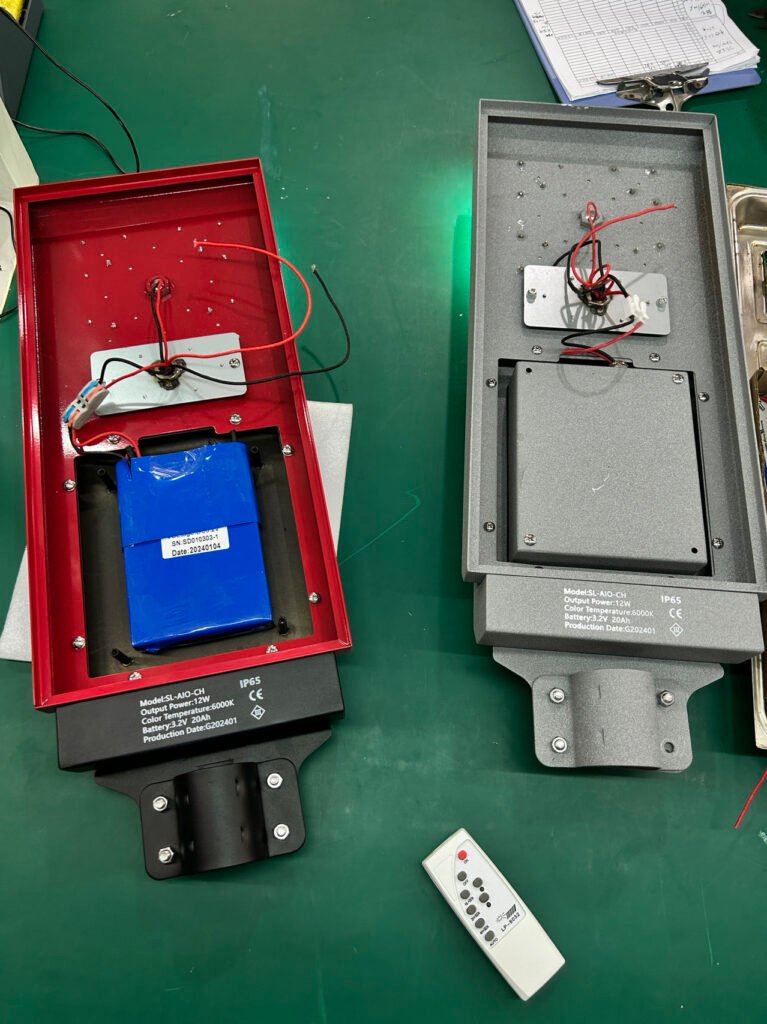
A well-designed solar lamp housing should include effective waterproofing (IP65 or IP66) and surface coating (GB/T9286 4B/5B standards) measures. The implementation method is as follows:
Waterproofing: All joints and openings of the enclosure should be designed with tight seals, and gaskets and coated with waterproof glue to prevent water ingress. Additionally, all electronic components should be adequately protected within a waterproof housing to ensure they function properly even in wet conditions.
- Scratch Resistance: The coating should have high scratch resistance to maintain its appearance and prevent wear and tear.
- Weather Resistance: Should be able to withstand prolonged exposure to sunlight, rain, and other environmental factors without fading or deterioration.
- Impact Resistance: The coating should be resistant to impacts and collisions to prevent damage to the casing.
- Smooth surface: A smooth surface is essential for ease of cleaning and maintenance, as well as aesthetic appearance.
By incorporating these features into the design and manufacturing process, solar light fixture housings can effectively withstand outdoor conditions while maintaining their functionality and appearance over time.
7. Solar Lights Use What Type of Wires Inside The Connecting Cables?
The connecting wires of solar lights usually use copper core or copper-clad aluminum core wires. These two materials have good electrical conductivity and corrosion resistance and are suitable for use in outdoor environments.
Among them, pure copper core wires have higher conductivity and corrosion resistance, but the cost is higher. Copper-clad aluminum core wires have a relatively low cost, but their electrical conductivity and corrosion resistance are slightly inferior to pure copper cores.
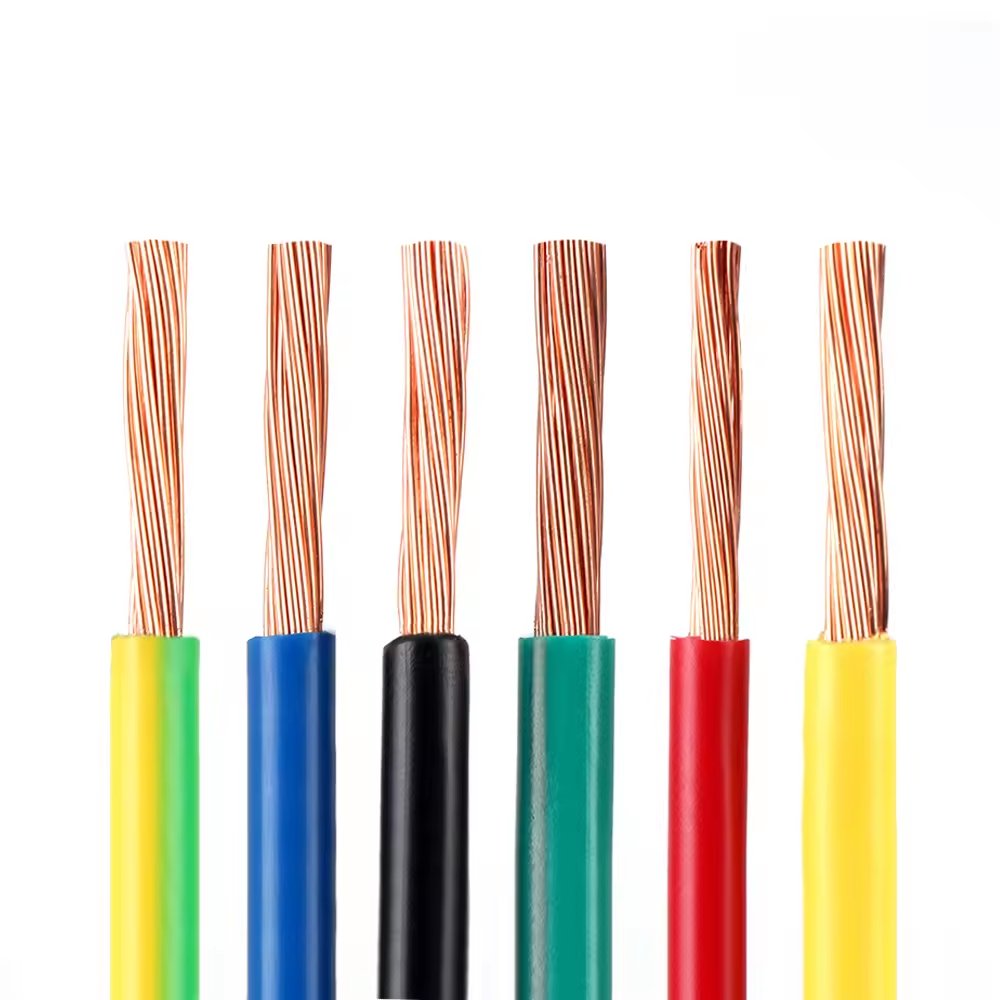
Pure copper core wires

Copper-clad aluminium wire
All the cables used by GCOTS are pure copper core cables, which are also determined by our product quality positioning.
Conclusion
In conclusion, understanding the quality of solar lights requires a comprehensive assessment of each component. Each of them plays a crucial role in determining the overall performance and reliability of the solar light system.
Key considerations include the charging capacity of the solar panel, battery capacity, matching and balancing, optical parameters of LED chips, quality of the lens and light fixture, and type of wires used in connecting cables. Testing procedures and tools such as electroluminescent equipment, integrated sphere testing, and spectroradiometers are essential for evaluating the quality and performance of solar light components.
By ensuring that each component meets quality standards and specifications, solar light manufacturers can deliver reliable and efficient lighting solutions for various applications. Collaborating with reputable suppliers and conducting thorough quality checks are essential steps in ensuring the durability and effectiveness of solar light systems.
2 Responses
Hey there, I love all the points you made on that topic. There is definitely a great deal to know about this subject, and with that said, feel free to visit my blog Webemail24 to learn more about Blogging.
Thx Felix.